BFT Group, Italy
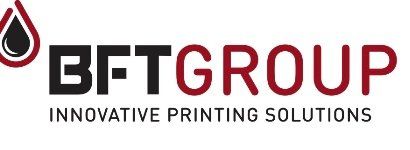
Integrated solutions and systems for flexographic printing.
For further information please contact Novasys, go to our download section or visit BFT Group's Website at: https://www.bftgroup.tech/index-en.php
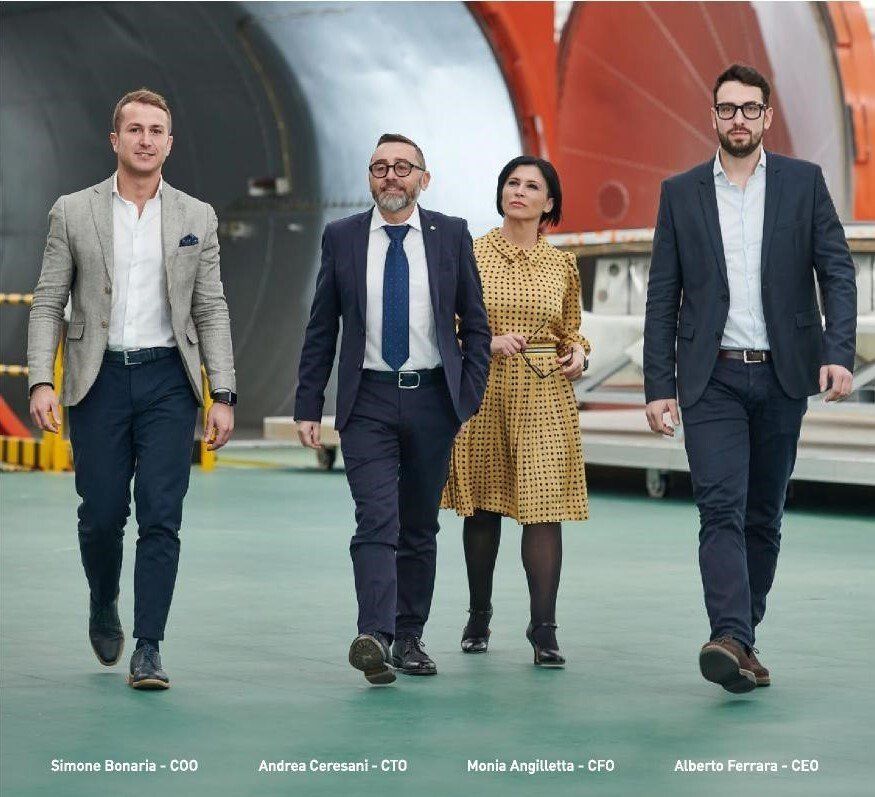
BFT is born out of the need for innovation on inking systems in the world of flexographic printing. Since most inking systems are manual and free of washing automations, operators must adjust the speed of the pumps and remove the ink bucket manually and insert a bucket of water in the washing phase.
For this, BFT has created the BFT Flexo inking and washing system and the BFT Carbon doctor blade unit. An integrated solution for your flexographic machines.
Two products to use separately, but. when integrated, achieve unparalleled levels of process optimisation. A flexible system. Just like the products you make.
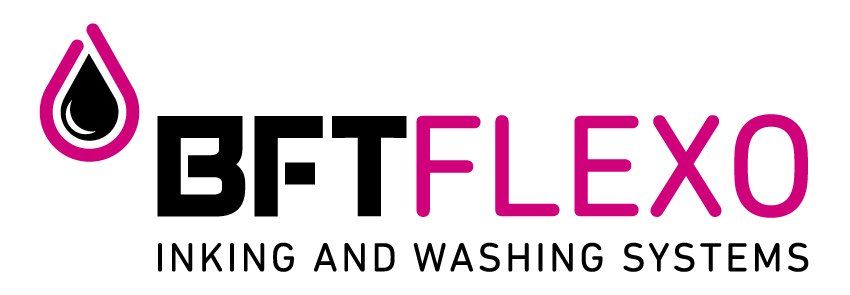
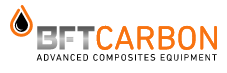
BFT is born out of the need for innovation on inking systems in the world of flexographic printing. Since most inking systems are manual and free of washing automations, operators must adjust the speed of the pumps and remove the ink bucket manually and insert a bucket of water in the washing phase.
For this, BFT has created the BFT Flexo inking and washing system and the BFT Carbon doctor blade unit. An integrated solution for your flexographic machines.
Two products to use separately, but. when integrated, achieve unparalleled levels of process optimisation. A flexible system. Just like the products you make.
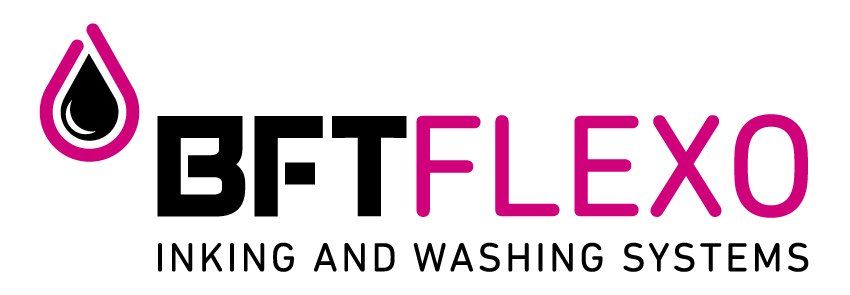
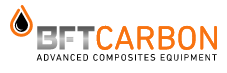
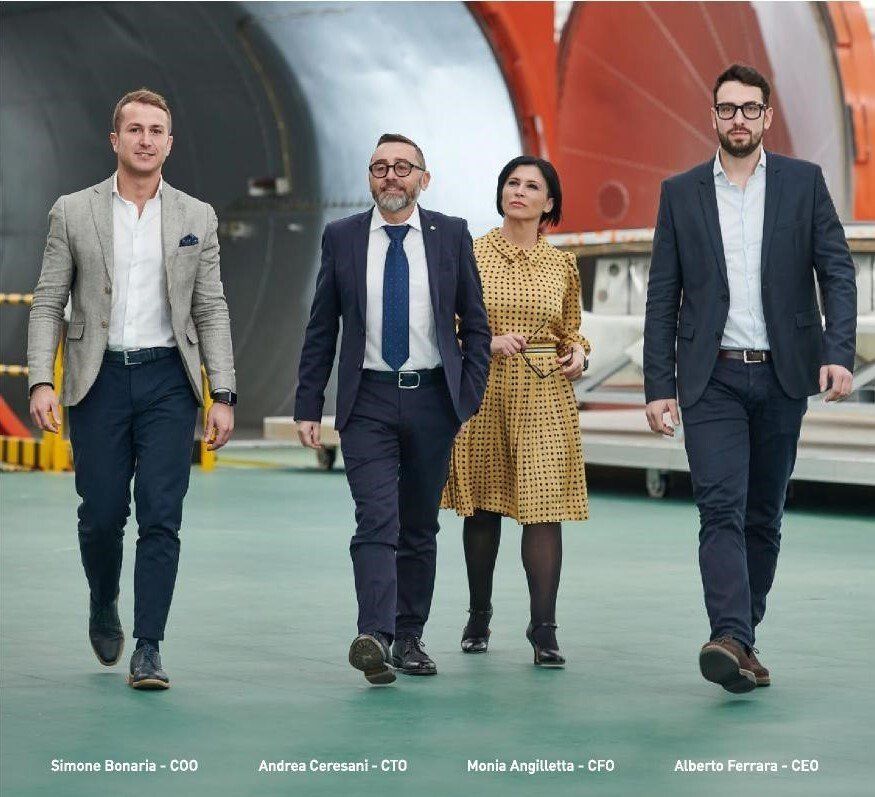
BFT is born out of the need for innovation on inking systems in the world of flexographic printing. Since most inking systems are manual and free of washing automations, operators must adjust the speed of the pumps and remove the ink bucket manually and insert a bucket of water in the washing phase.
For this, BFT has created the BFT Flexo inking and washing system and the BFT Carbon doctor blade unit. An integrated solution for your flexographic machines.
Two products to use separately, but. when integrated, achieve unparalleled levels of process optimisation. A flexible system. Just like the products you make.
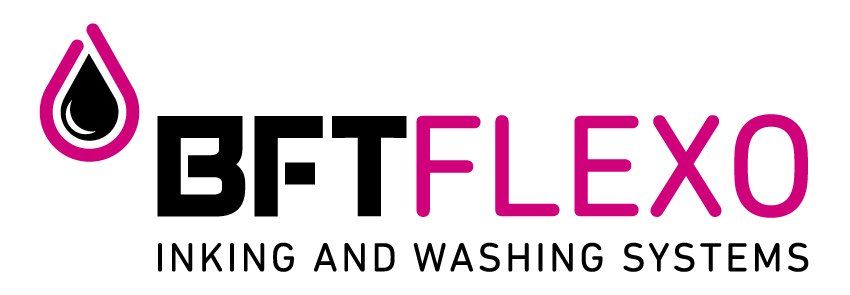
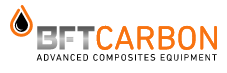
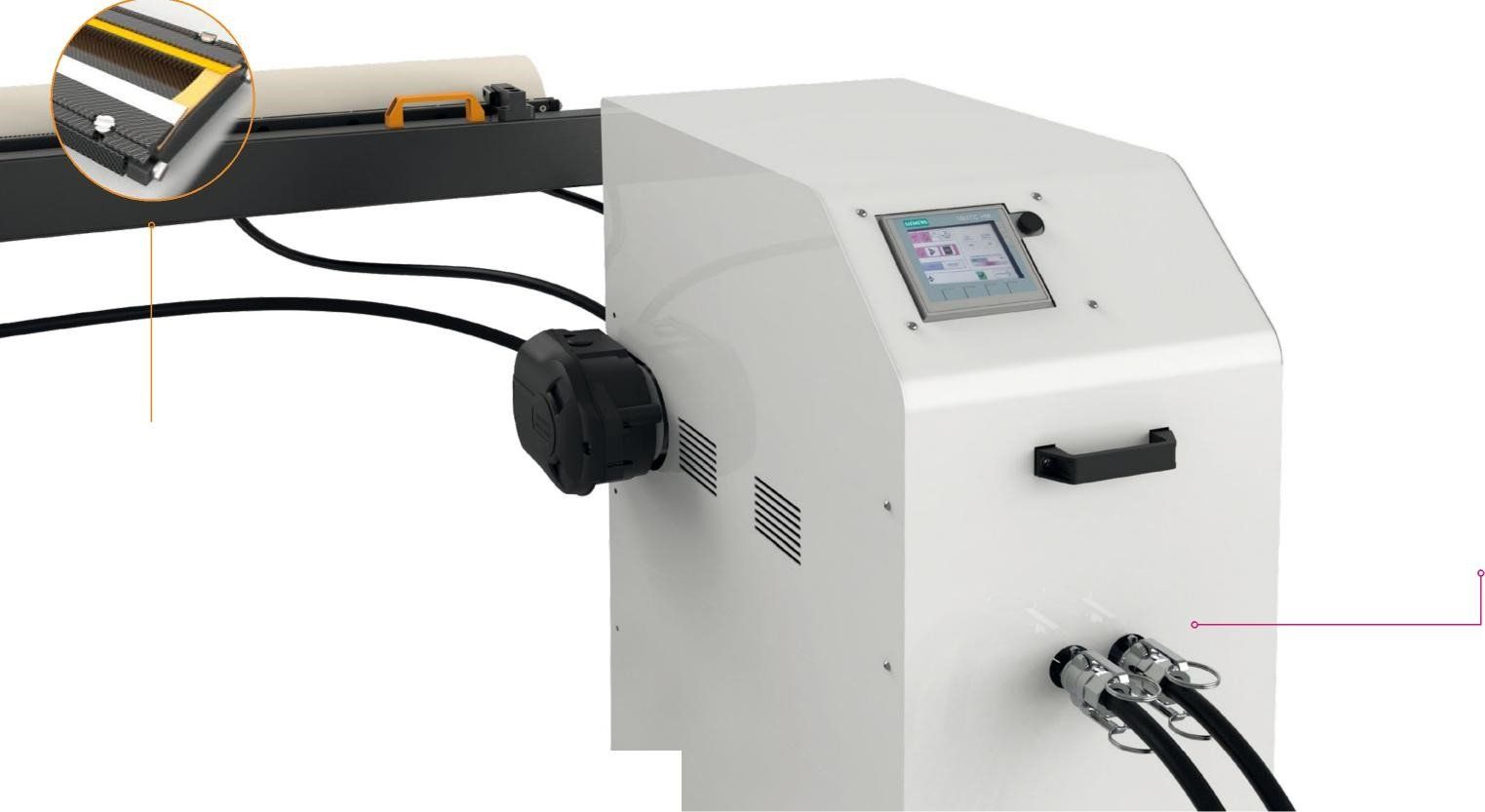
It automates the inking and washing processes, recovering ink and halving consumption
Thanks to the excellent results obtained by the printing customers, the BFT Flexo systems are requested as an original equipment even by OEMs, that find technology and reliability in BFT Flexo systems but also a considerable saving compared to the internal management of the washing system.
The carbon doctor
blade unit, easy to wash and install
A BFT complete inking system (inking
and washing system + doctor blade unit)
solution is also required by the OEMs.
Always looking for innovation for
its products, BFT Carbon is born,
a cutting-edge product made of carbon
fibre, with sensors inside that communicate
with the BFT Flexo system to optimise
the process at best.
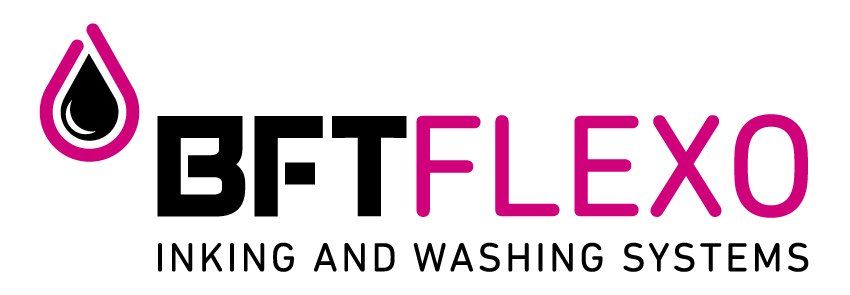
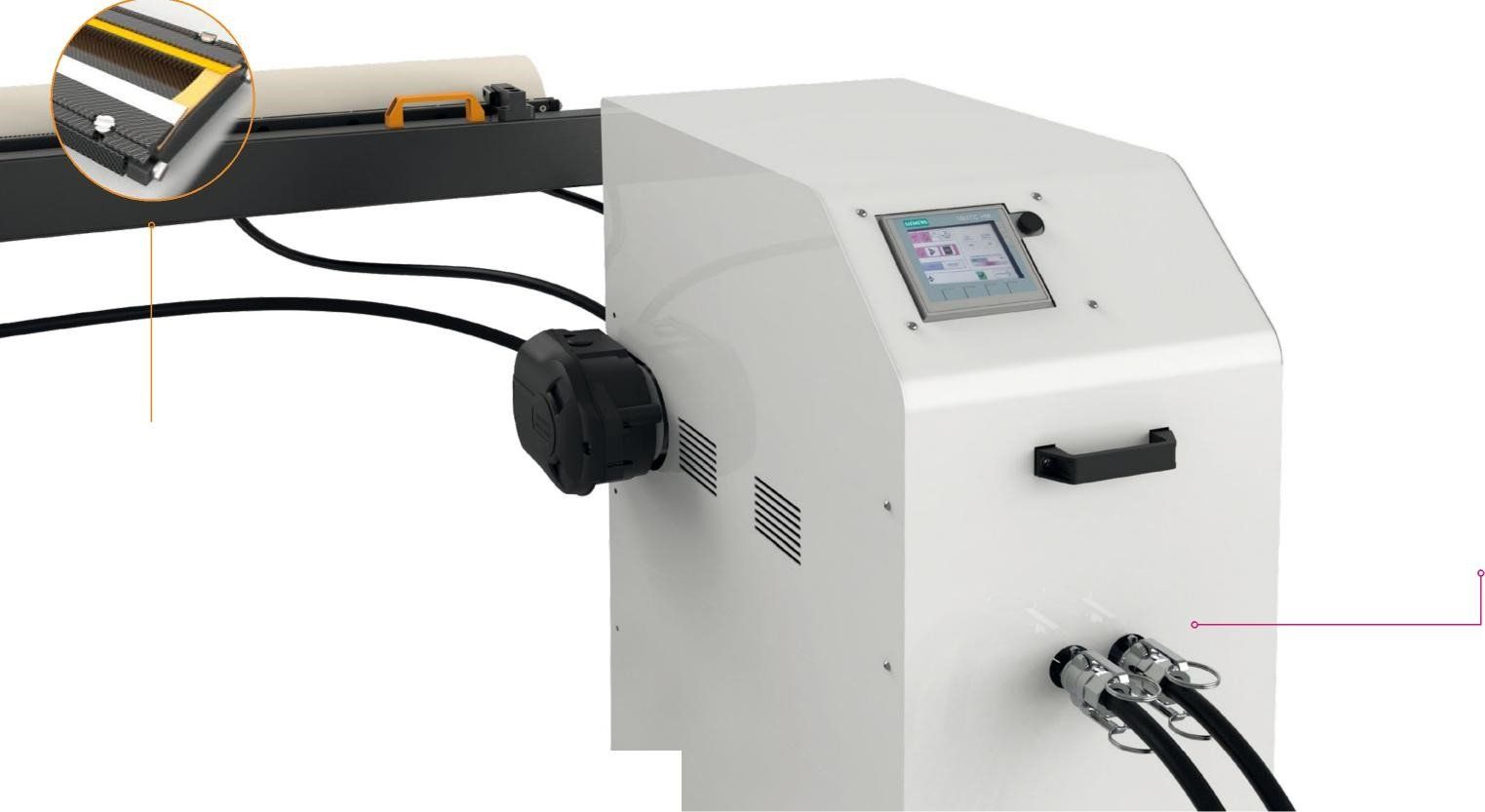
It automates the inking and washing processes, recovering ink and halving consumption
Thanks to the excellent results obtained by the printing customers, the BFT Flexo systems are requested as an original equipment even by OEMs, that find technology and reliability in BFT Flexo systems but also a considerable saving compared to the internal management of the washing system.
The carbon doctor
blade unit, easy to wash and install
A BFT complete inking system (inking and washing system + doctor blade unit) solution is also required by the OEMs.
Always looking for innovation for its products, BFT Carbon is born, a cutting-edge product made of carbon fibre, with sensors inside that communicate with the BFT Flexo system to optimise the process at best.
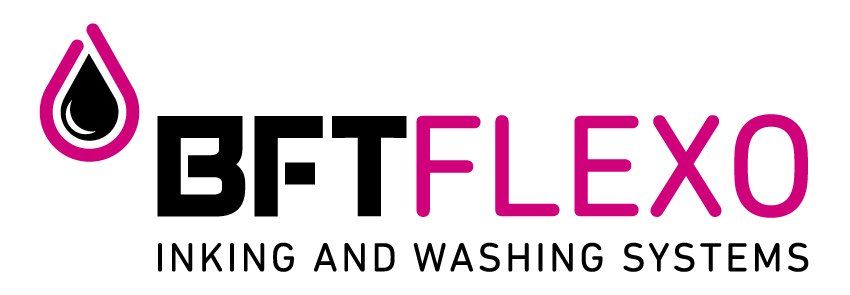
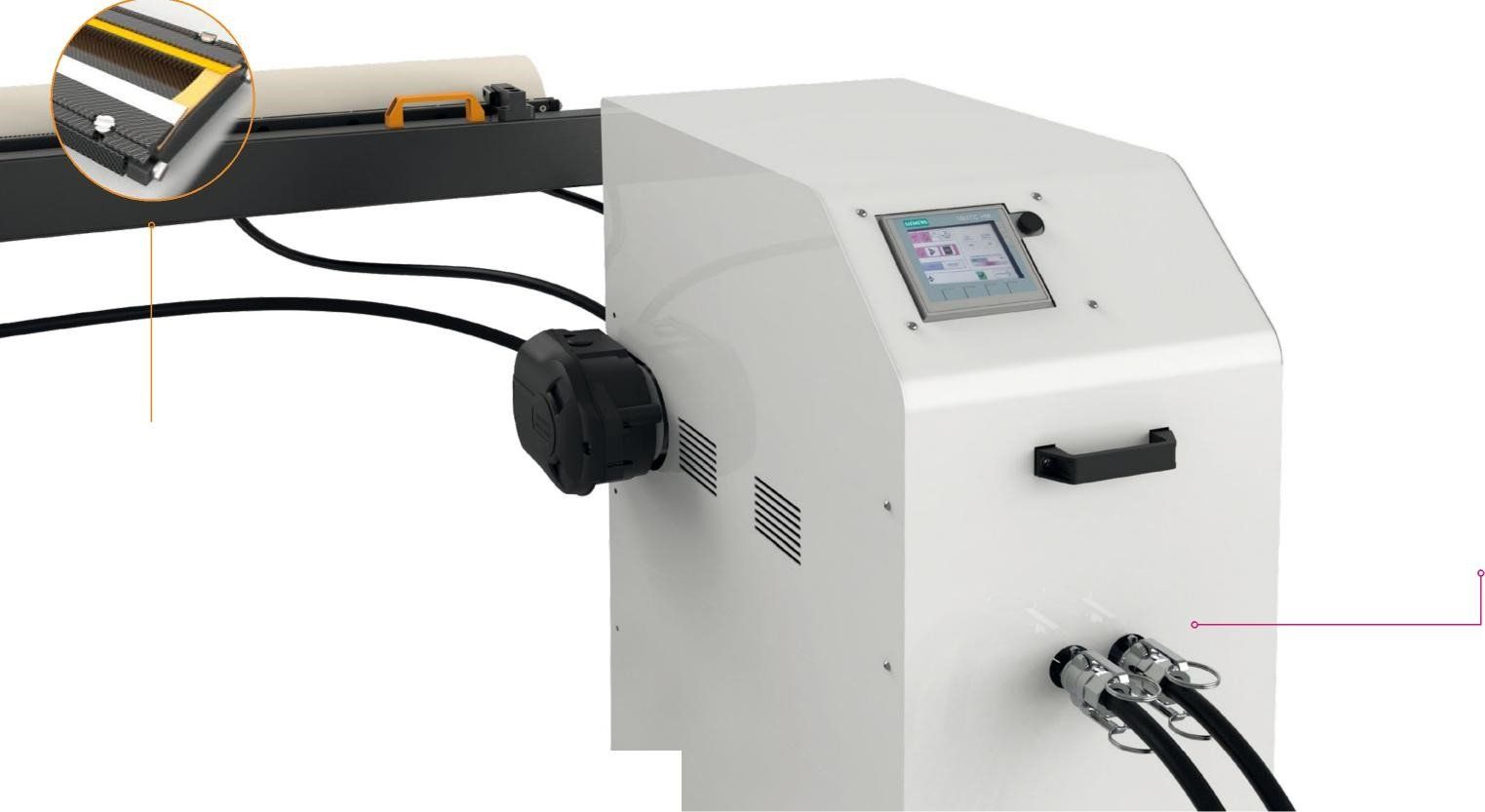
It automates the inking and washing processes, recovering ink and halving consumption
Thanks to the excellent results obtained by the printing customers, the BFT Flexo systems are requested as an original equipment even by OEMs, that find technology and reliability in BFT Flexo systems but also a considerable saving compared to the internal management of the washing system.
The carbon doctor
blade unit, easy to wash and install
A BFT complete inking system (inking
and washing system + doctor blade unit)
solution is also required by the OEMs.
Always looking for innovation for
its products, BFT Carbon is born,
a cutting-edge product made of carbon
fibre, with sensors inside that communicate
with the BFT Flexo system to optimise
the process at best.
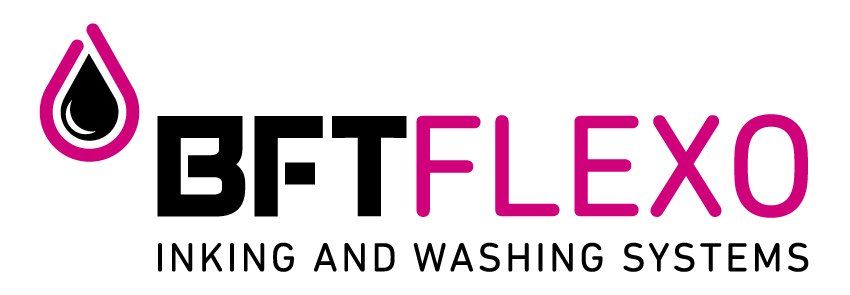
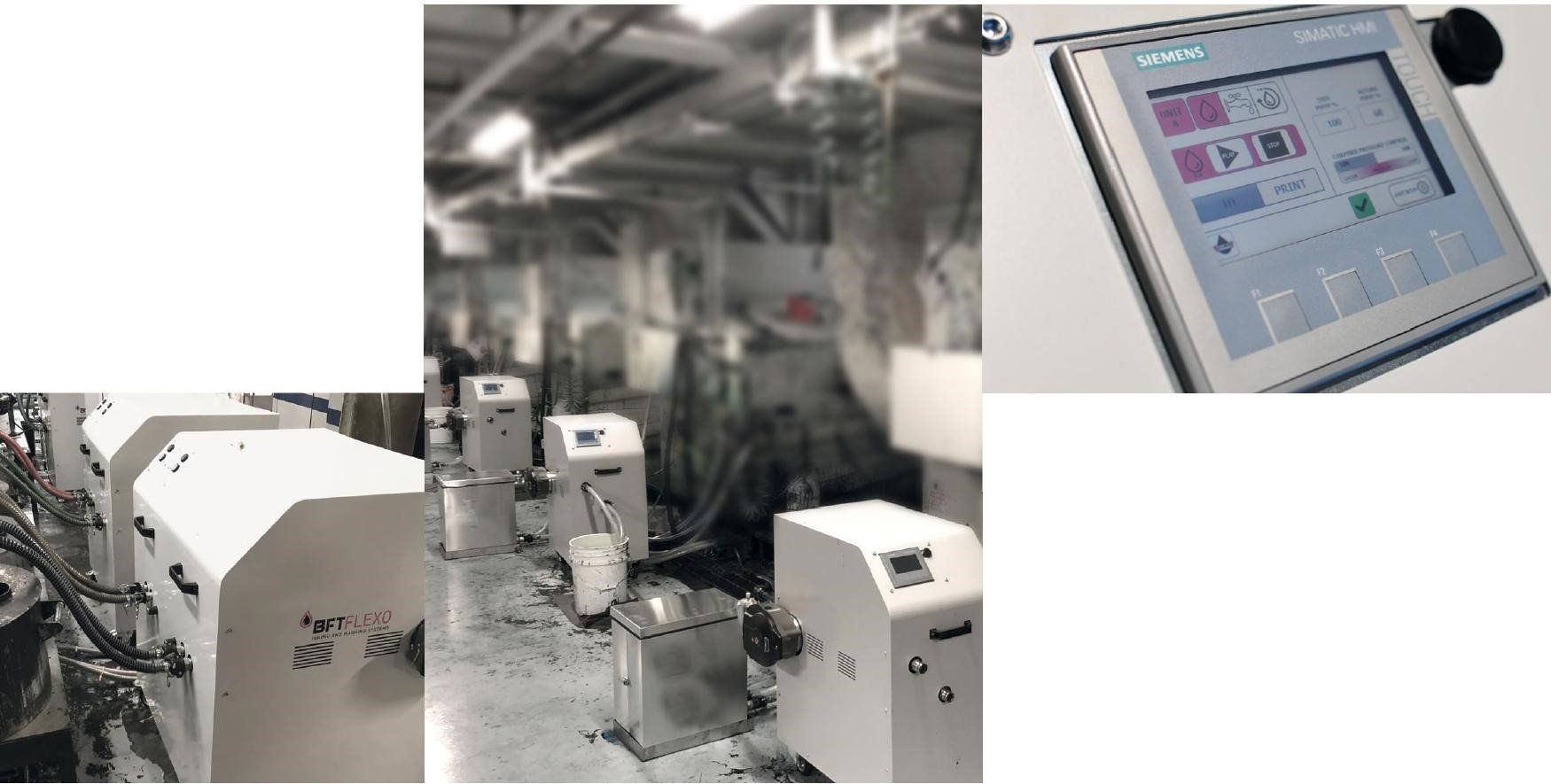
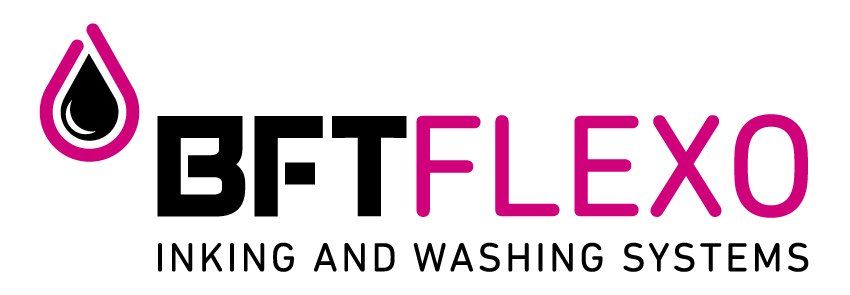
The only thing you need to do by hand is touching the screen
Most inking systems include manual processes, including the pump adjustment and washing. Operations that require prolonged machine downtime and a continuous assistance by the staff.
The BFT FLEXO systems are completely automatic: to start any cycle, just press a buttonon the touch screen.
It remembers
everything you do
Process standardisation
The operator can easily set the speed of the pumps from the screen to optimise the inking phase and the washing phase. Setting is saved and linked to the order to be resumed over time.
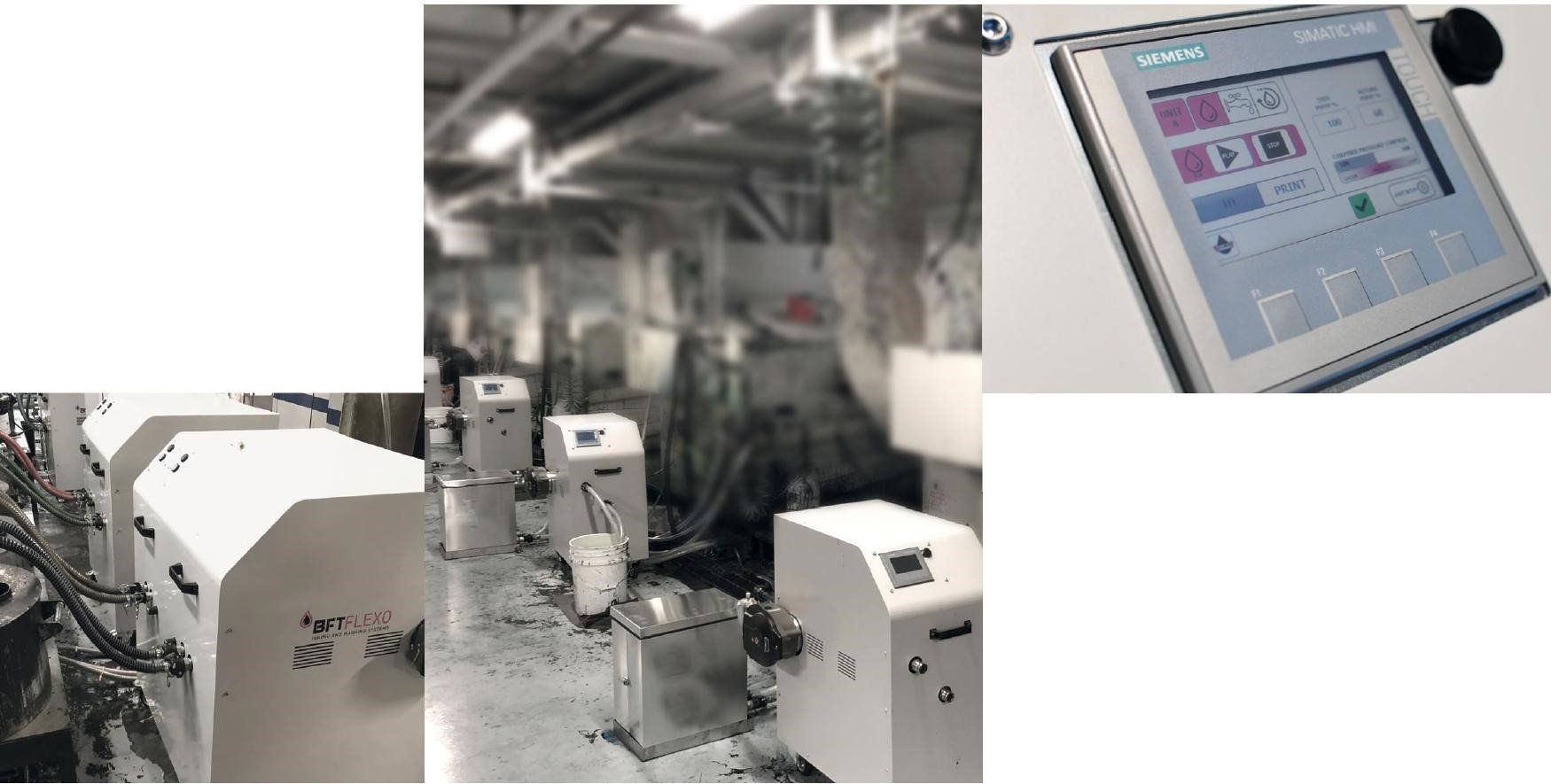
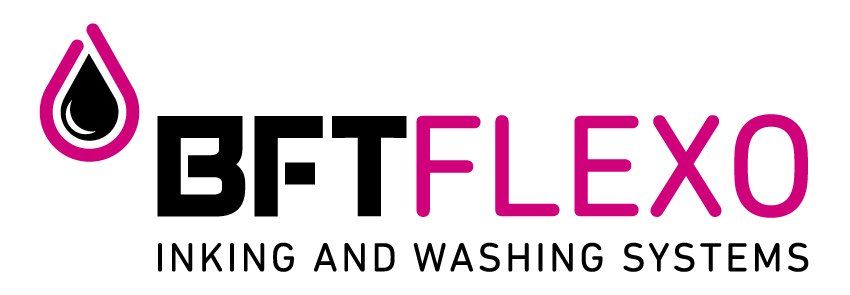
The only thing you need to do by hand is touching the screen
Most inking systems include manual processes, including the pump adjustment and washing. Operations that require prolonged machine downtime and a continuous assistance by the staff.
The BFT FLEXO systems are completely automatic: to start any cycle, just press a buttonon the touch screen.
It remembers
everything you do
Process standardisation
The operator can easily set the speed of the pumps from the screen to optimise the inking phase and the washing phase. Setting is saved and linked to the order to be resumed over time.
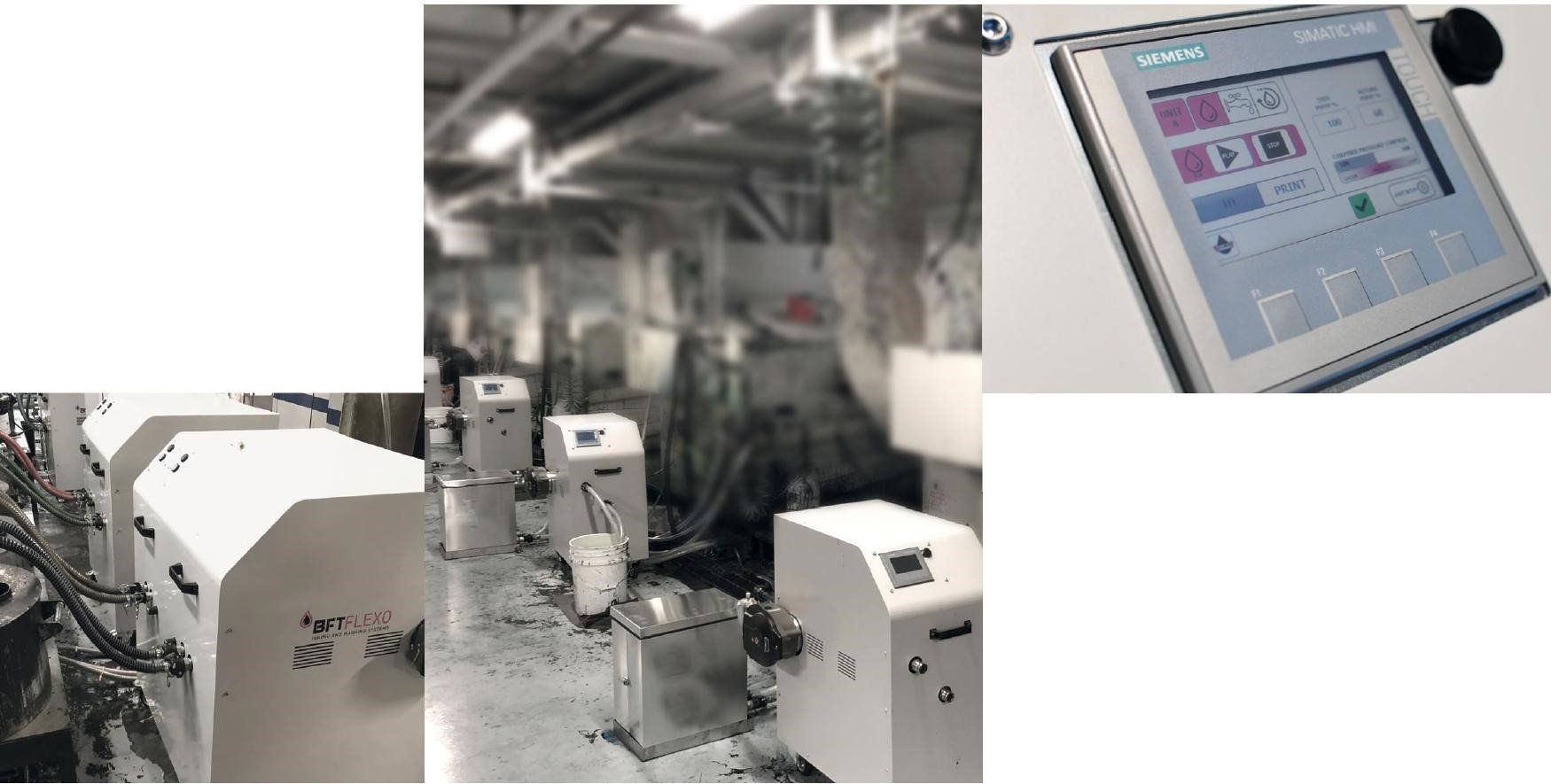
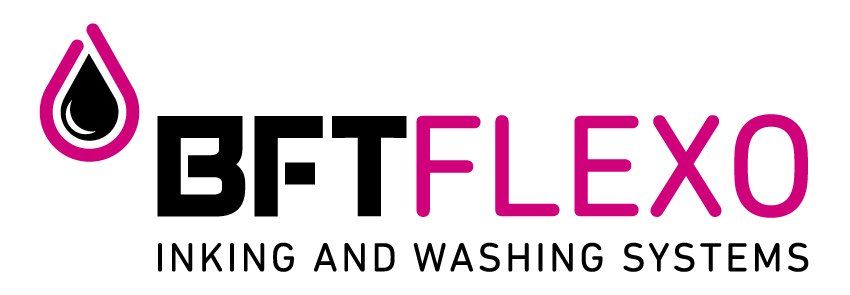
The only thing you need to do by hand is touching the screen
Most inking systems include manual processes, including the pump adjustment and washing. Operations that require prolonged machine downtime and a continuous assistance by the staff.
The BFT FLEXO systems are completely automatic: to start any cycle, just press a buttonon the touch screen.
It remembers
everything you do
Process standardisation
The operator can easily set the speed of the pumps from the screen to optimise the inking phase and the washing phase. Setting is saved and linked to the order to be resumed over time.
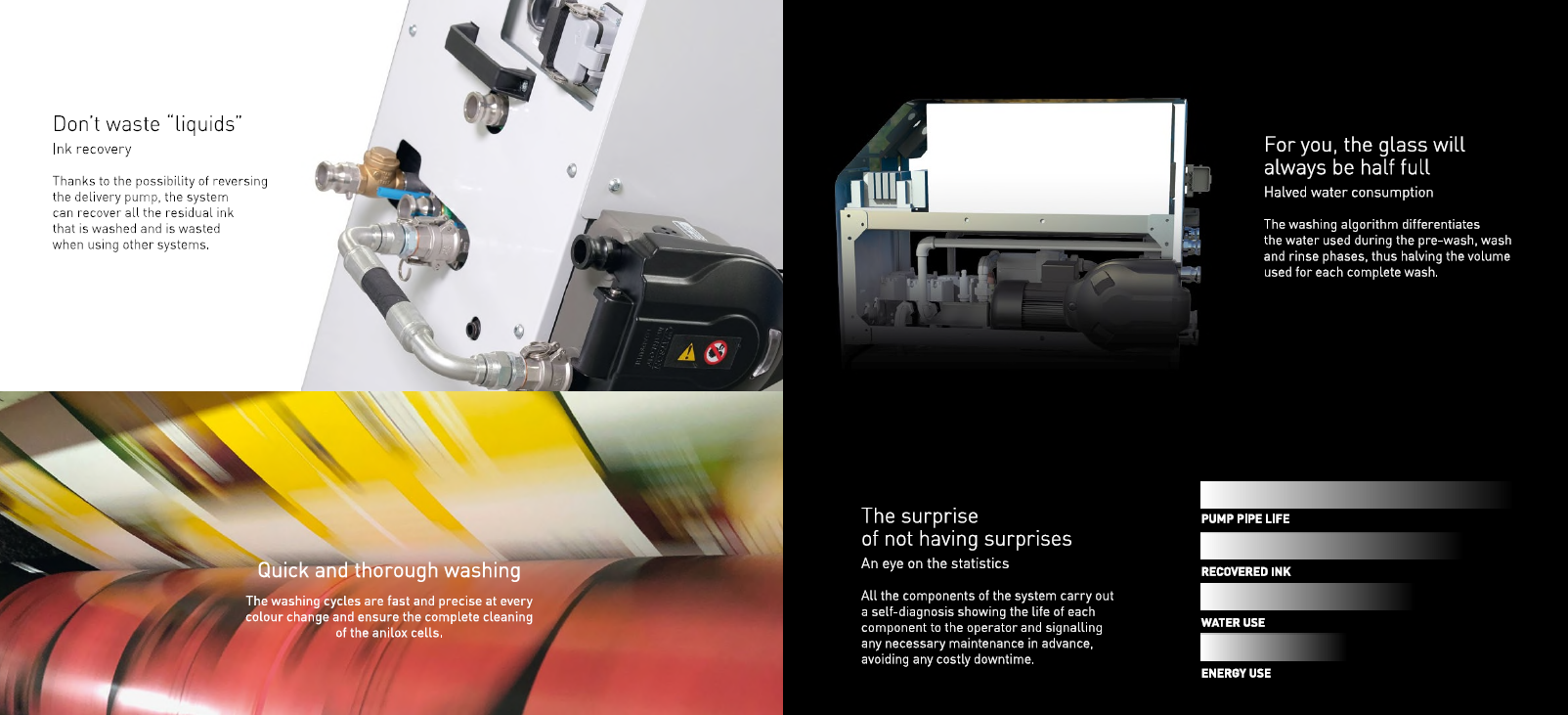
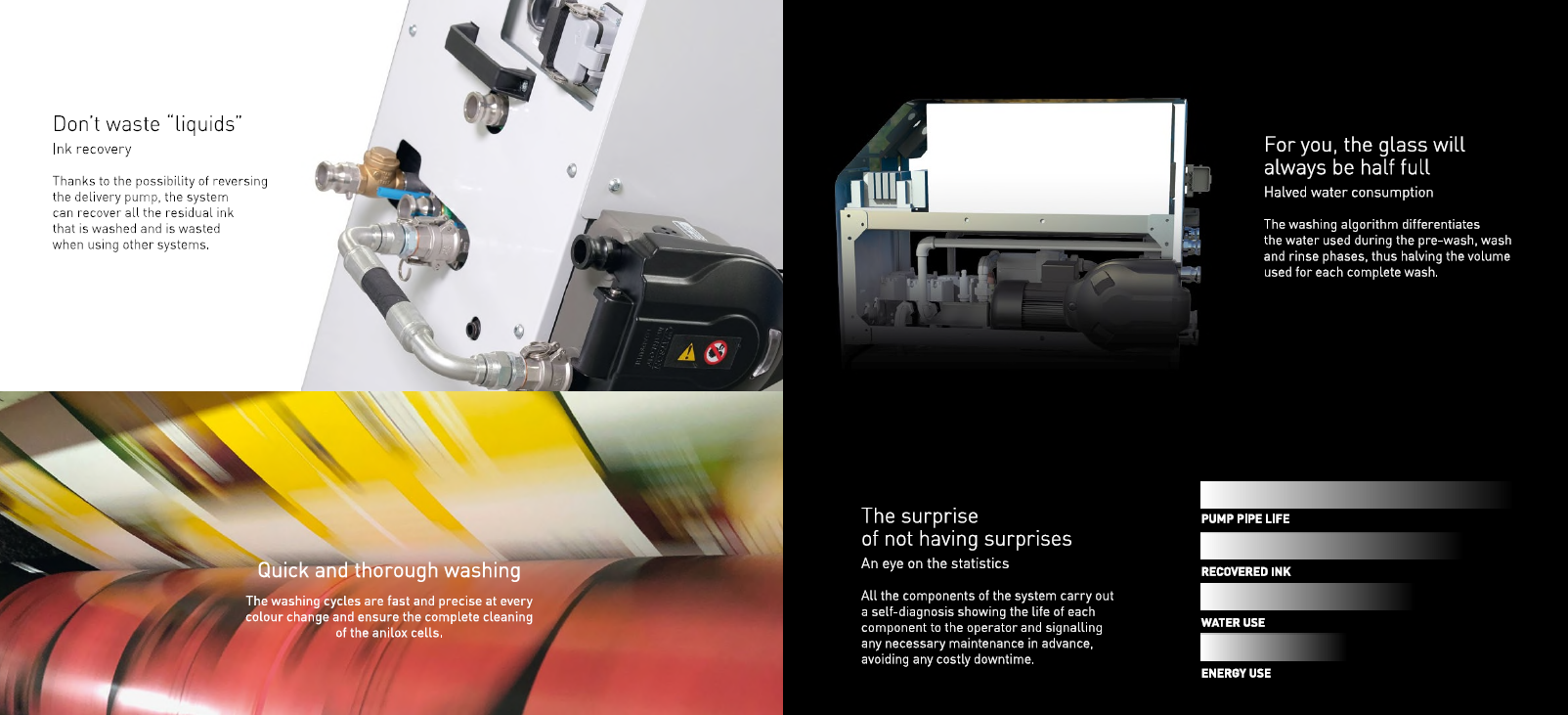
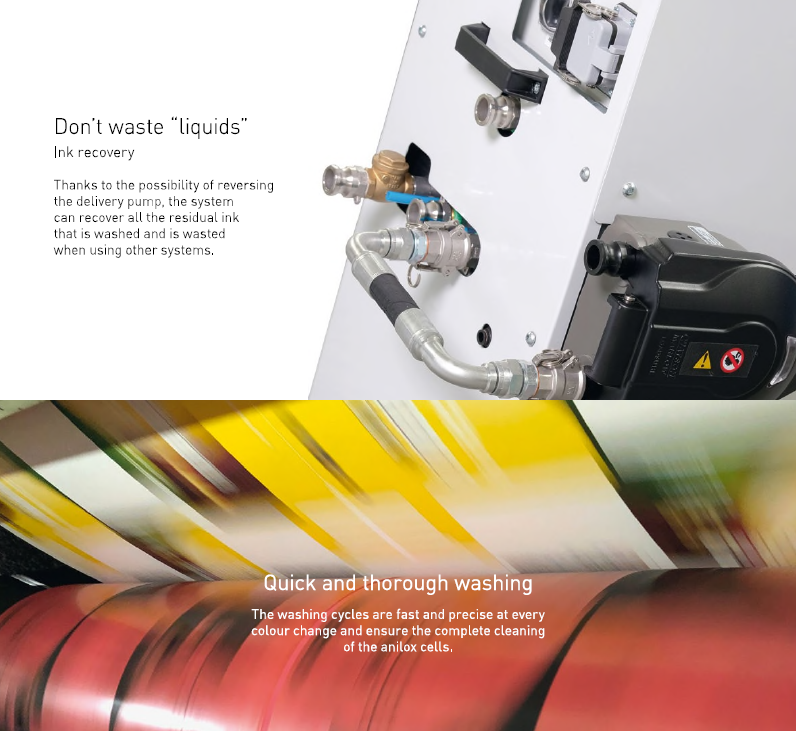
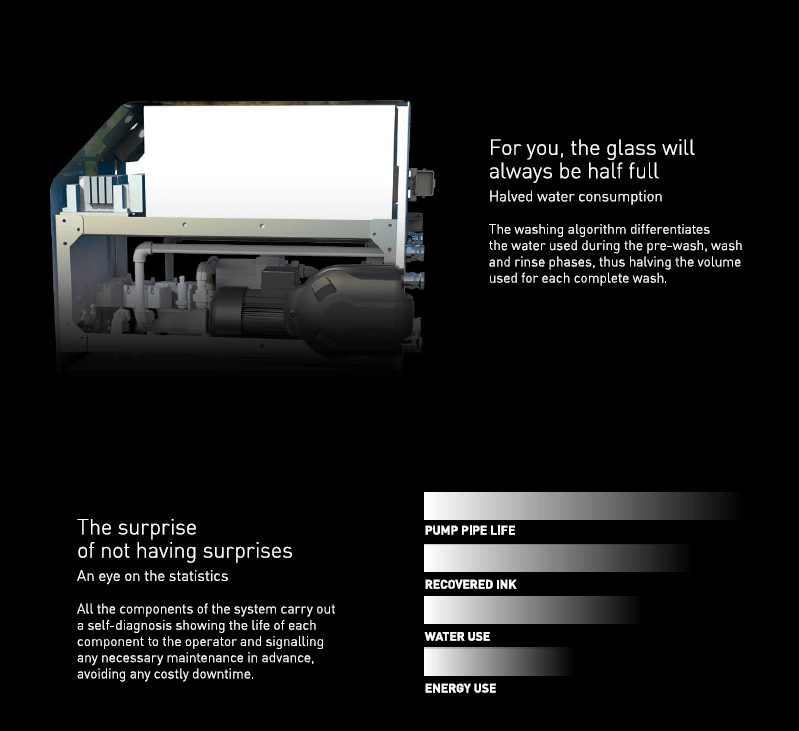
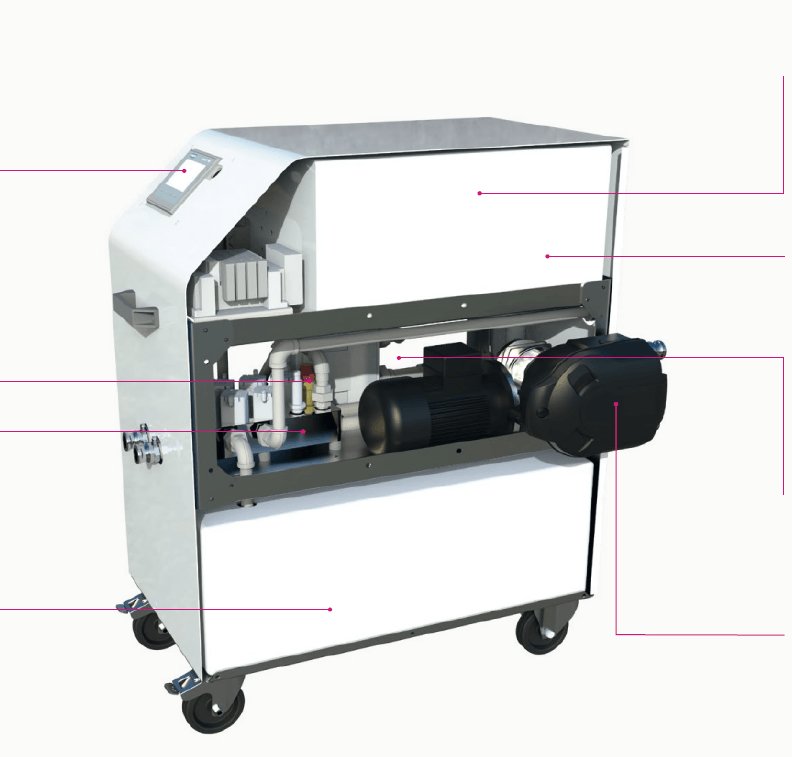
Technical Features
Touch Screen
for easy and immediate settings, it allows standardising the pump settings and many other parameters
Sensors
air pressure. PH. viscosity, temperature
BFf FLEXO Manifold
a single stainless-steel component is the heart of the system
InternaL tank to save 50% of water
with the same washing quality without the use of the tank
Components
all the system components supplied by our partners are available allover the world for immediate assistance
PLC SIEMENS
arranged to interface the printing machine
with an integrated teleservice system
Algorithm for the Internal washing of the system
to clean each component
and avoid blocking and malfunctioning
PP and STAINLESS pipes
polypropylene welded tubes
to guarantee the absence of internal leaks
and the maximum compatibility with solvents
Peristaltic pump
reduces pulse to improve print quality,
does not contaminate the product, allows
scheduled maintenance and consumption
is lower than air pumps
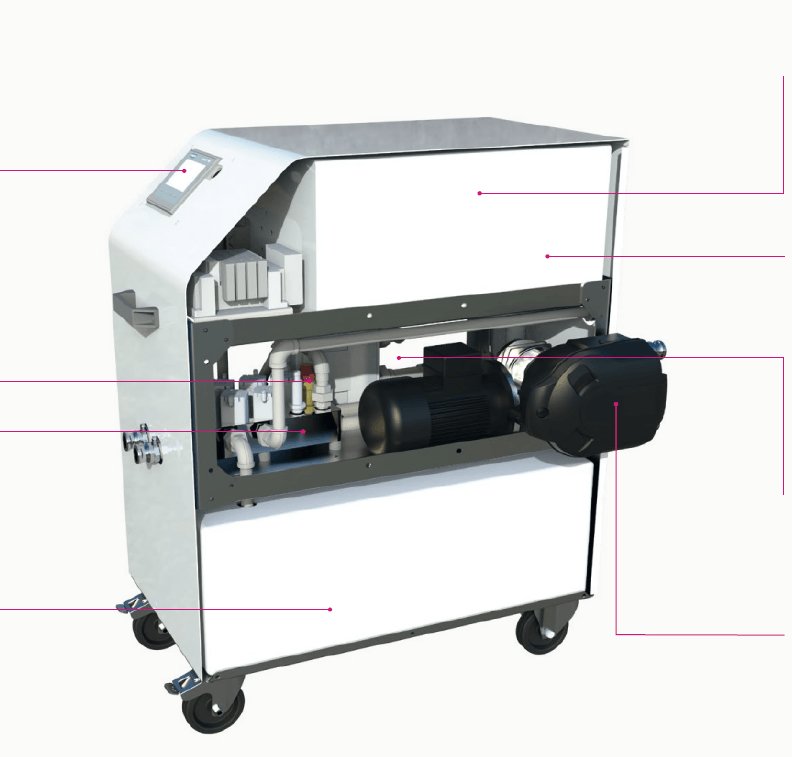
Technical Features
Touch Screen
for easy and immediate settings, it allows standardising the pump settings and many other parameters
Sensors
air pressure. PH. viscosity, temperature
BFf FLEXO Manifold
a single stainless-steel component is the heart of the system
InternaL tank to save 50% of water
with the same washing quality without the use of the tank
Components
all the system components supplied by our partners are available allover the world for immediate assistance
PLC SIEMENS
arranged to interface the printing machine
with an integrated teleservice system
Algorithm for the Internal washing of the system
to clean each component
and avoid blocking and malfunctioning
PP and STAINLESS pipes
polypropylene welded tubes
to guarantee the absence of internal leaks
and the maximum compatibility with solvents
Peristaltic pump
reduces pulse to improve print quality,
does not contaminate the product, allows
scheduled maintenance and consumption
is lower than air pumps
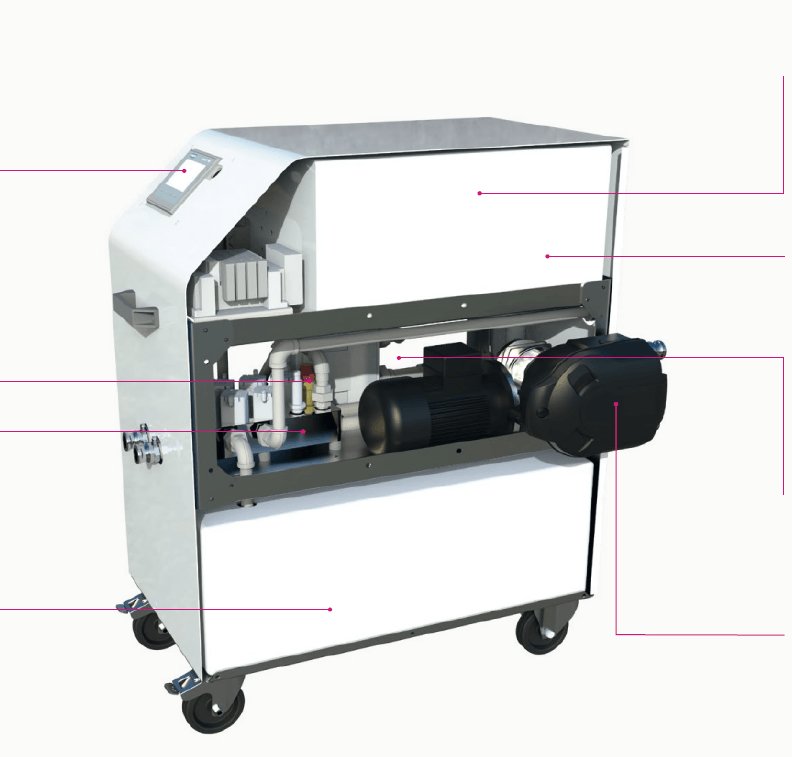
Technical Features
Touch Screen
for easy and immediate settings, it allows standardising the pump settings and many other parameters
Sensors
air pressure. PH. viscosity, temperature
BFf FLEXO Manifold
a single stainless-steel component is the heart of the system
InternaL tank to save 50% of water
with the same washing quality without the use of the tank
Components
all the system components supplied by our partners are available allover the world for immediate assistance
PLC SIEMENS
arranged to interface the printing machine
with an integrated teleservice system
Algorithm for the Internal washing of the system
to clean each component
and avoid blocking and malfunctioning
PP and STAINLESS pipes
polypropylene welded tubes
to guarantee the absence of internal leaks
and the maximum compatibility with solvents
Peristaltic pump
reduces pulse to improve print quality,
does not contaminate the product, allows
scheduled maintenance and consumption
is lower than air pumps

Description of the system
Pulse Free Inking
inking is managed by a peristaltic pump that reduces the pulsations to a minimum and a return pump to increase the ink circulation speed and avoid getting in the doctor blade unit
Ink Recovery
The system recovers ink from both pipes, allowing the maximum ink saving
Pre-washing and washing with 50% water saving
Using an internal tank to store the water resulting from the test washing cycle, the system uses the same water twice in order to use half the watervolume. The cycle ends with the cleaning of the circuit using clean water or solvent to avoid contamination in the subsequent printing operation
Range
BFT systems can be equipped with pump combinations requested by the customer:
1P - Single membrane pump
2P- Double peristaltic
PM - Peristaltic + membrane pump
2M - Double Membrane pumps
Sectors
Flexography
Rotogravure
Offset
Fluids
Water based inks
Solvent based inks (ATEX)
Varnishes
UV ink
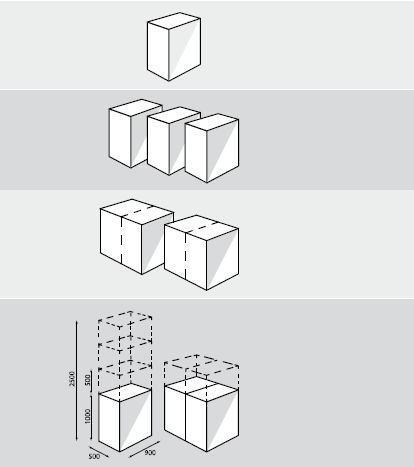
Configurations
GT1
Stand-alone system with integrated PLCfor single
applications, coatings and carte
GTX - L
Master and slave system up to 10 units for in-Line printing machines
GTX - 2C1
CiMaster and slave System in two-colour groups
compactness and ease forthe maintenance
of machines with a central drum
GTX - CUSTOM
Master and slave system in multiple configurations depending on the client's space for every typeof central drum machine
Other Functions:
Internal Cleaning Algorithm
At the end of the task, the operator starts a cycle to wash all the system's valves and pumps. and washes the two bucket connection pipes internally, this waythe BFT machine is completely clean and ready forthe next job by postponing maintenance
Diagnostics and Statistics
The sensor implemented systems can self-diagnose problems and create statistics related to the work that is carried out and that can be used when
the same order is repeated or to define the process standardisation by fixing all those variables neglected in a printing process until now.
Checking the Ink Temperature
Temperature is viscosity's
most important variable. Keeping the ink temperature constant allows avoiding constantviscosity corrections by the operator and standardiseen undervalued parameter at the same time.

Description of the system
Pulse Free Inking
inking is managed by a peristaltic pump that reduces the pulsations to a minimum and a return pump to increase the ink circulation speed and avoid getting in the doctor blade unit
Ink Recovery
The system recovers ink from both pipes, allowing the maximum ink saving
Pre-washing and washing with 50% water saving
Using an internal tank to store the water resulting from the test washing cycle, the system uses the same water twice in order to use half the watervolume. The cycle ends with the cleaning of the circuit using clean water or solvent to avoid contamination in the subsequent printing operation
Range
BFT systems can be equipped with pump combinations requested by the customer:
1P - Single membrane pump
2P- Double peristaltic
PM - Peristaltic + membrane pump
2M - Double Membrane pumps
Sectors
Flexography
Rotogravure
Offset
Fluids
Water based inks
Solvent based inks (ATEX)
Varnishes
UV ink
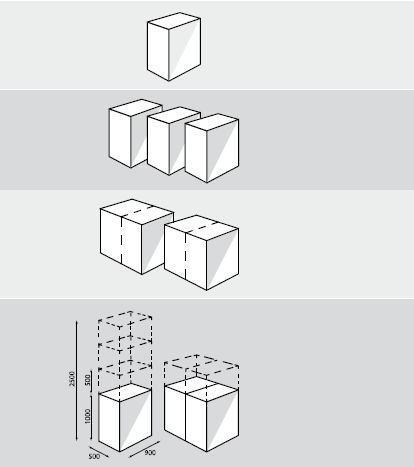
Configurations
GT1
Stand-alone system with integrated PLCfor single applications, coatings and carte
GTX - L
Master and slave system up to 10 units for in-Line printing machines
GTX - 2C1
CiMaster and slave System in two-colour groups compactness and ease forthe maintenance of machines with a central drum
GTX - CUSTOM
Master and slave system in multiple configurations depending on the client's space for every typeof central drum machine
Other Functions:
Internal Cleaning Algorithm
At the end of the task, the operator starts a cycle to wash all the system's valves and pumps. and washes the two bucket connection pipes internally, this waythe BFT machine is completely clean and ready forthe next job by postponing maintenance
Diagnostics and Statistics
The sensor implemented systems can self-diagnose problems and create statistics related to the work that is carried out and that can be used when
the same order is repeated or to define the process standardisation by fixing all those variables neglected in a printing process until now.
Checking the Ink Temperature
Temperature is viscosity's
most important variable. Keeping the ink temperature constant allows avoiding constantviscosity corrections by the operator and standardiseen undervalued parameter at the same time.

Description of the system
Pulse Free Inking
inking is managed by a peristaltic pump that reduces the pulsations to a minimum and a return pump to increase the ink circulation speed and avoid getting in the doctor blade unit
Ink Recovery
The system recovers ink from both pipes, allowing the maximum ink saving
Pre-washing and washing with 50% water saving
Using an internal tank to store the water resulting from the test washing cycle, the system uses the same water twice in order to use half the watervolume. The cycle ends with the cleaning of the circuit using clean water or solvent to avoid contamination in the subsequent printing operation
Range
BFT systems can be equipped with pump combinations requested by the customer:
1P - Single membrane pump
2P- Double peristaltic
PM - Peristaltic + membrane pump
2M - Double Membrane pumps
Sectors
Flexography
Rotogravure
Offset
Fluids
Water based inks
Solvent based inks (ATEX)
Varnishes
UV ink
Configurations
GT1
Stand-alone system with integrated PLCfor single
applications, coatings and carte
GTX - L
Master and slave system up to 10 units for in-Line printing machines
GTX - 2C1
CiMaster and salve System in two-colour groups
compactness and ease forthe maintenance
of machines with a central drum
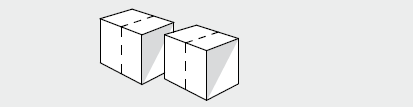
GTX - CUSTOM
Master and slave system in multiple configurations depending on the client's space for every typeof central drum machine
Other Functions:
Internal Cleaning Algorithm
At the end of the task, the operator starts a cycle to wash all the system's valves and pumps. and washes the two bucket connection pipes internally, this waythe BFT machine is completely clean and ready forthe next job by postponing maintenance
Diagnostics and Statistics
The sensor implemented systems can self-diagnose problems and create statistics related to the work that is carried out and that can be used when
the same order is repeated or to define the process standardisation by fixing all those variables neglected in a printing process until now.
Checking the Ink Temperature
Temperature is viscosity's
most important variable. Keeping the ink temperature constant allows avoiding constantviscosity corrections by the operator and standardiseen undervalued parameter at the same time.
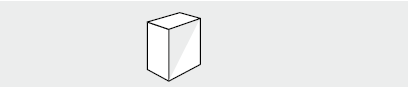
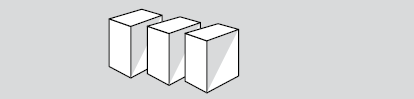
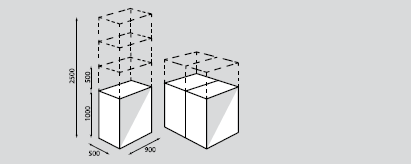
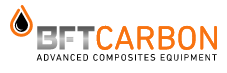
Increasing efficiency is not a detail, but often a detail makes the difference
Most doctor blade units are made in aluminium. Water-based inks affect the surface, corroding it. BFT Carbon, developed in carbon, guarantees a surface as new even after ten years of use.
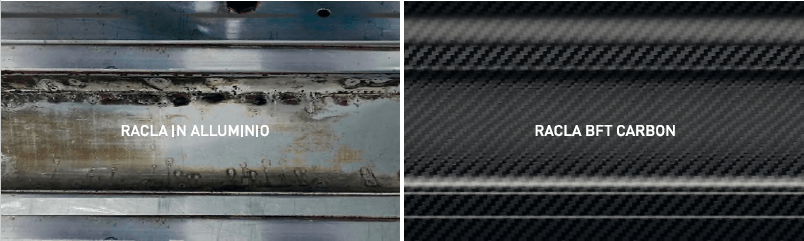
State of materials after ten years of use
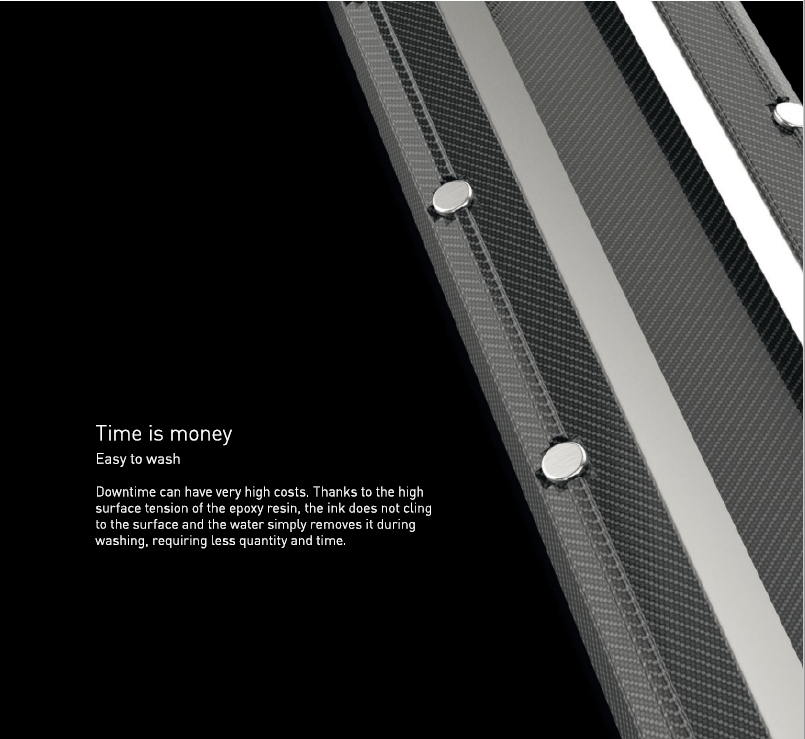
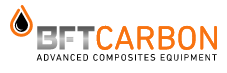
Increasing efficiency is not a detail, but often a detail makes the difference
Most doctor blade units are made in aluminium. Water-based inks affect the surface, corroding it. BFT Carbon, developed in carbon, guarantees a surface as new even after ten years of use.
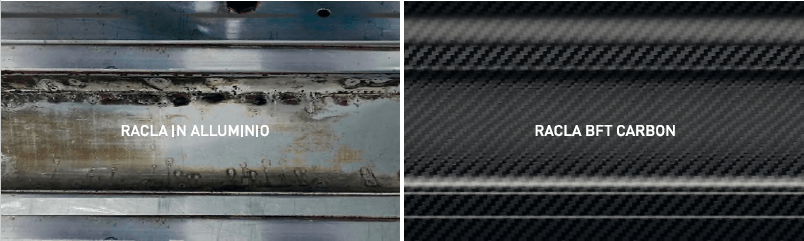
State of materials after ten years of use
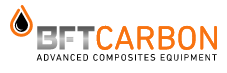
Increasing efficiency is not a detail, but often a detail makes the difference
Most doctor blade units are made in aluminium. Water-based inks affect the surface, corroding it. BFT Carbon, developed in carbon, guarantees a surface as new even after ten years of use.
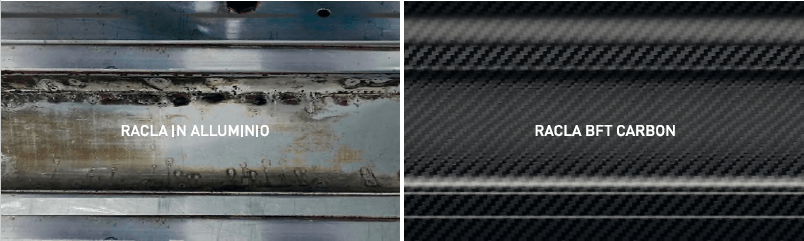
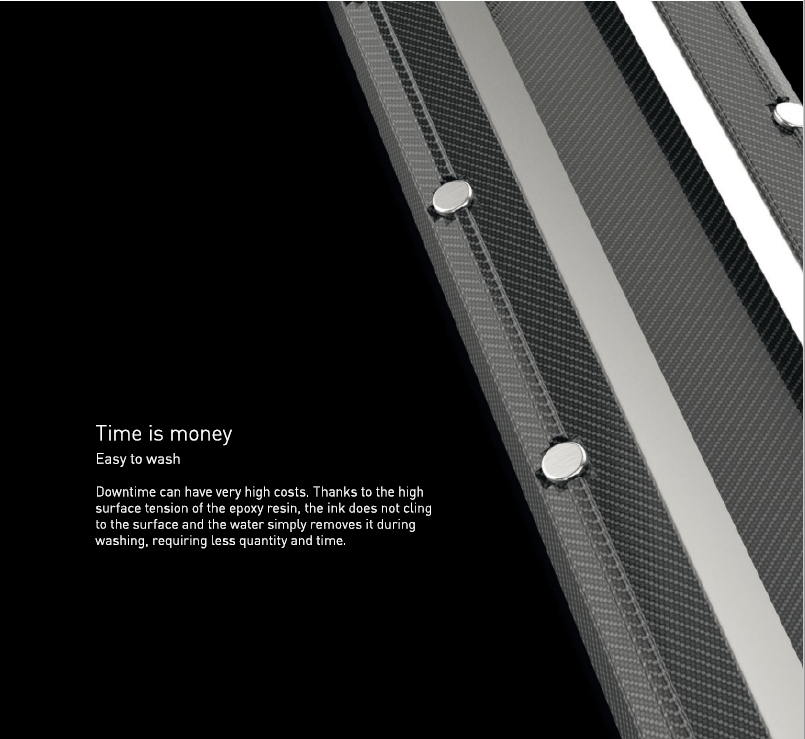
State of materials after ten years of use
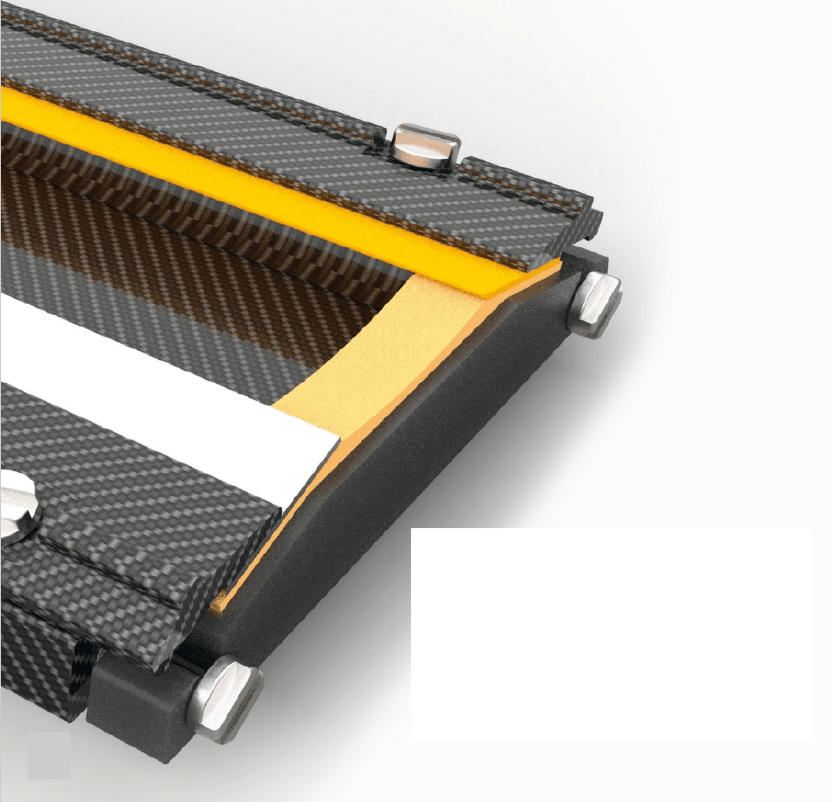
Such an easy task
Easy handling
Carbon is an ultra-light material and facilitates the installation and movement of the doctor blade unit. Unlike aluminium systems that require two people for handling, BFT Carbon just needs one operator.
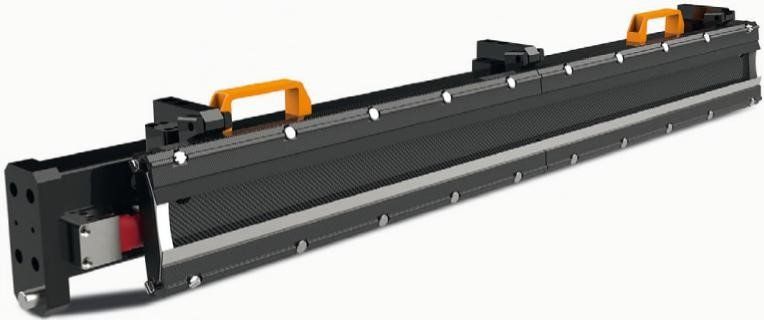
"Made to measure" is our standard
The different profiles are specially designed for every type of application, from inking to coating. BFT creates made-to-measure profiles at the customer's request and converts doctor blade units in aluminium
with state-of-the-art carbon fibre units.
BFT CARBON: IS BUILT AND ASSEMBLED INTERNALLY,
ENSURING SAVINGS UP TO 30%
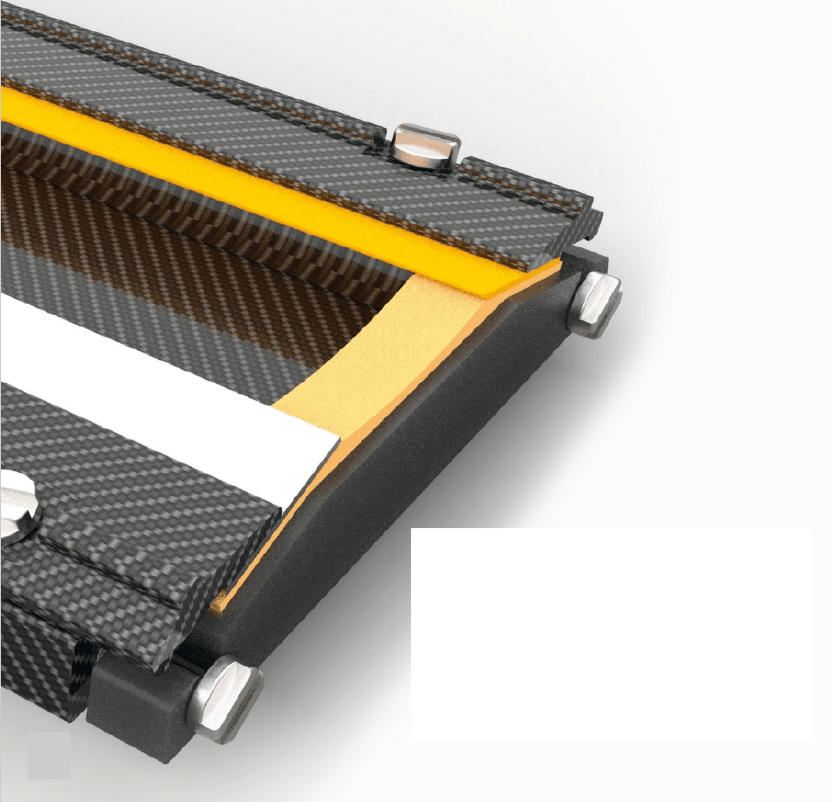
Such an easy task
Easy handling
Carbon is an ultra-light material and facilitates the installation and movement of the doctor blade unit. Unlike aluminium systems that require two people for handling, BFT Carbon just needs one operator.
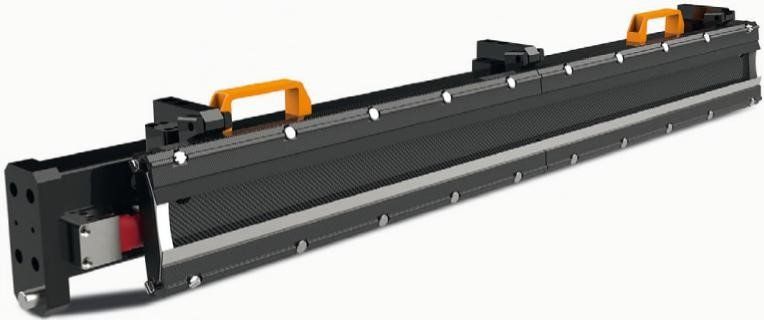
"Made to measure" is our standard
The different profiles are specially designed for every type of application, from inking to coating. BFT creates made-to-measure profiles at the customer's request and converts doctor blade units in aluminium
with state-of-the-art carbon fibre units.
BFT CARBON: IS BUILT AND ASSEMBLED INTERNALLY,
ENSURING SAVINGS UP TO 30%
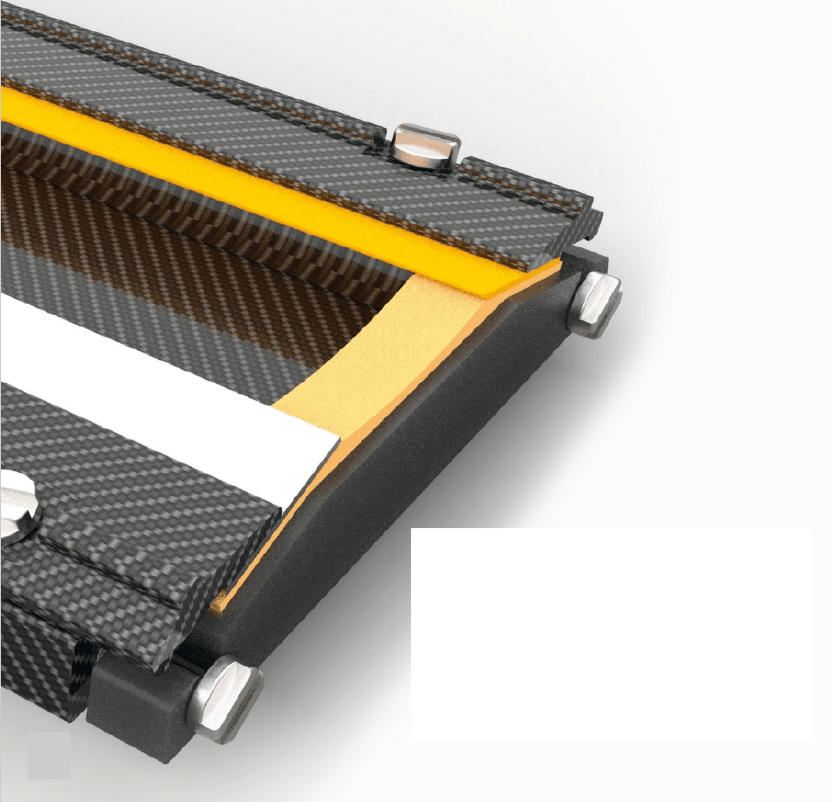
Such an easy task
Easy handling
Carbon is an ultra-light material and facilitates the installation and movement of the doctor blade unit. Unlike aluminium systems that require two people for handling, BFT Carbon just needs one operator.
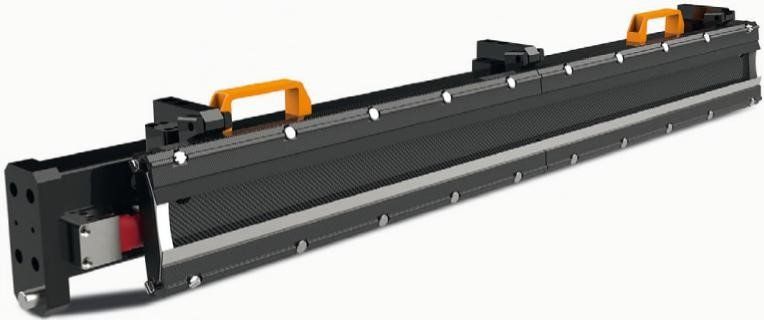
"Made to measure" is our standard
The different profiles are specially designed for every type of application, from inking to coating. BFT creates made-to-measure profiles at the customer's request and converts doctor blade units in aluminium
with state-of-the-art carbon fibre units.
BFT CARBON: IS BUILT AND ASSEMBLED INTERNALLY,
ENSURING SAVINGS UP TO 30%
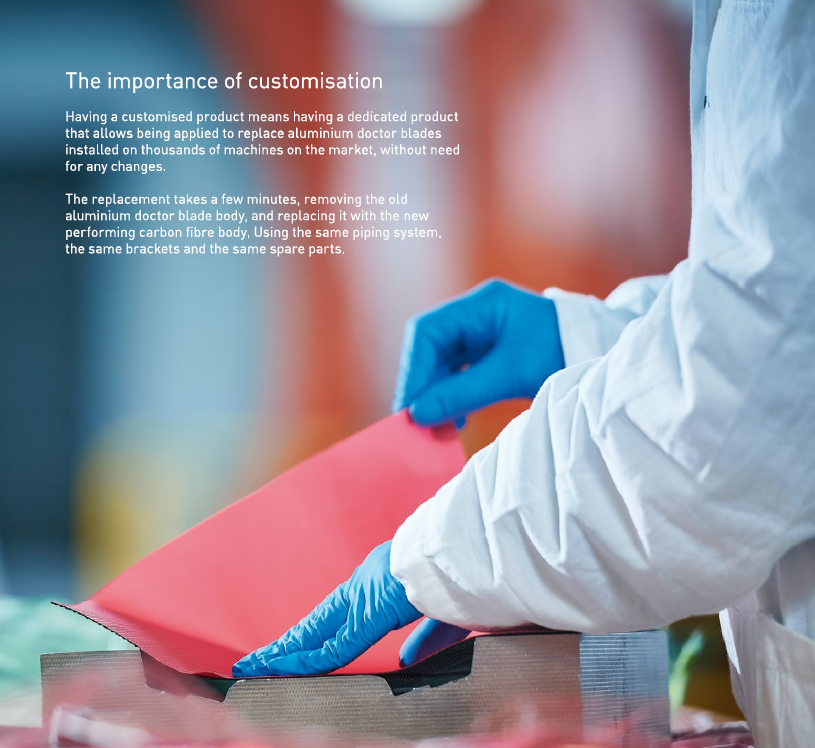
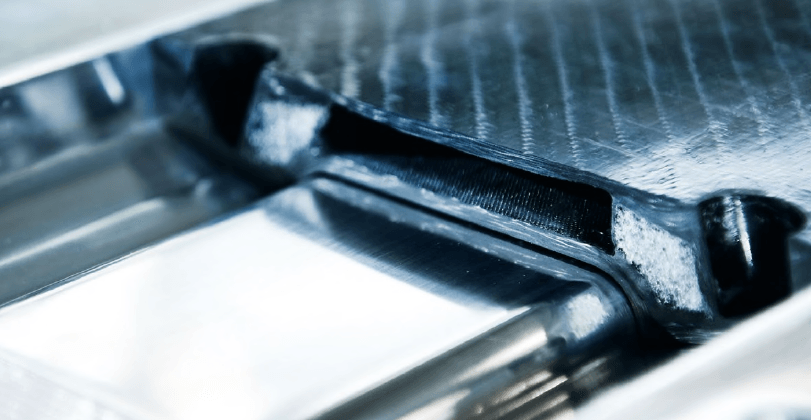
A revolution in 3 phases
Design
Every single project has a dedicated design part that includes the reverse engineering part to acquire all the measurements of the machine on which it will be installed if the printing machine is already in use; the 3D design part to design the system and integrate it inside the machine, and the phase in which each system component is placed an the counter with a specific coding.
Construction
Each part of the system is carefully constructed with the best quality standards to guarantee a high-quality system upon completion of the assembly process. Internal quality control ensures that every detail meets the necessary construction requirements. During the assembly, all the details are checked using the KanBan method to optimise the construction process, without any unexpected events.
Installation
The installation phase, and the one that completes the customisation process, involves the installation on the machine, making it unnecessary to modify the machine, thus allowing an easy and quick installation without any long and costly downtime.
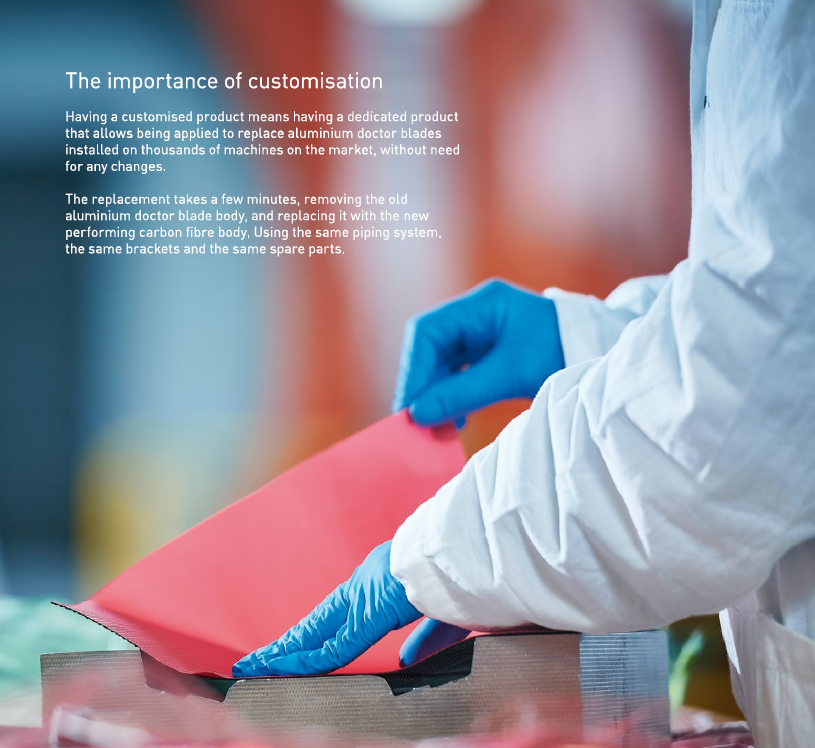
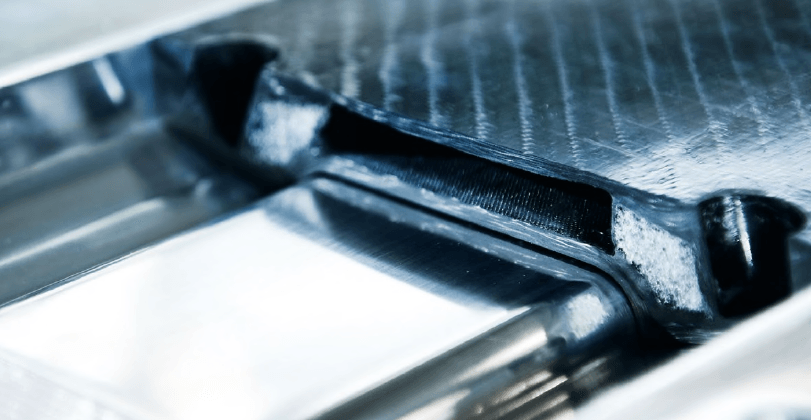
A revolution in 3 phases
Design
Every single project has a dedicated design part that includes the reverse engineering part to acquire all the measurements of the machine on which it will be installed if the printing machine is already in use; the 3D design part to design the system and integrate it inside the machine, and the phase in which each system component is placed an the counter with a specific coding.
Construction
Each part of the system is carefully constructed with the best quality standards to guarantee a high-quality system upon completion of the assembly process. Internal quality control ensures that every detail meets the necessary construction requirements. During the assembly, all the details are checked using the KanBan method to optimise the construction process, without any unexpected events.
Installation
The installation phase, and the one that completes the customisation process, involves the installation on the machine, making it unnecessary to modify the machine, thus allowing an easy and quick installation without any long and costly downtime.
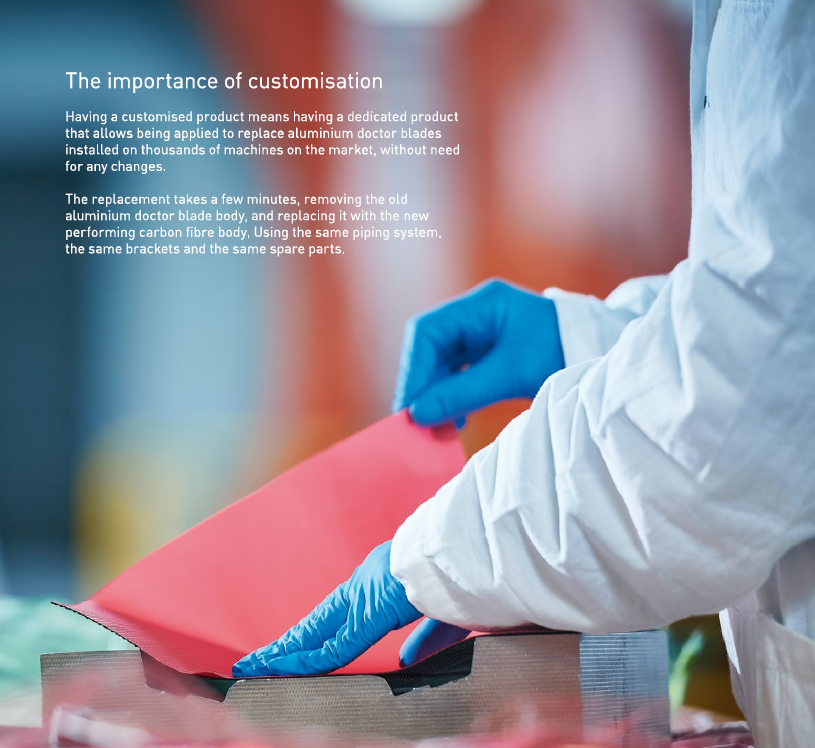
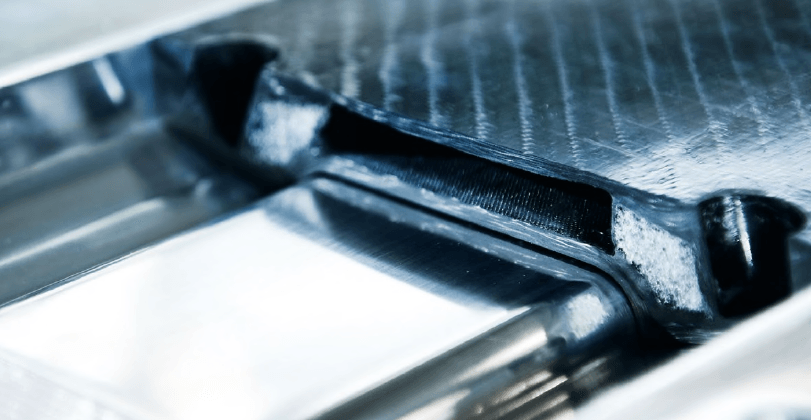
A revolution in 3 phases
Design
Every single project has a dedicated design part that includes the reverse engineering part to acquire all the measurements of the machine on which it will be installed if the printing machine is already in use; the 3D design part to design the system and integrate it inside the machine, and the phase in which each system component is placed an the counter with a specific coding.
Construction
Each part of the system is carefully constructed with the best quality standards to guarantee a high-quality system upon completion of the assembly process. Internal quality control ensures that every detail meets the necessary construction requirements. During the assembly, all the details are checked using the KanBan method to optimise the construction process, without any unexpected events.
Installation
The installation phase, and the one that completes the customisation process, involves the installation on the machine, making it unnecessary to modify the machine, thus allowing an easy and quick installation without any long and costly downtime.
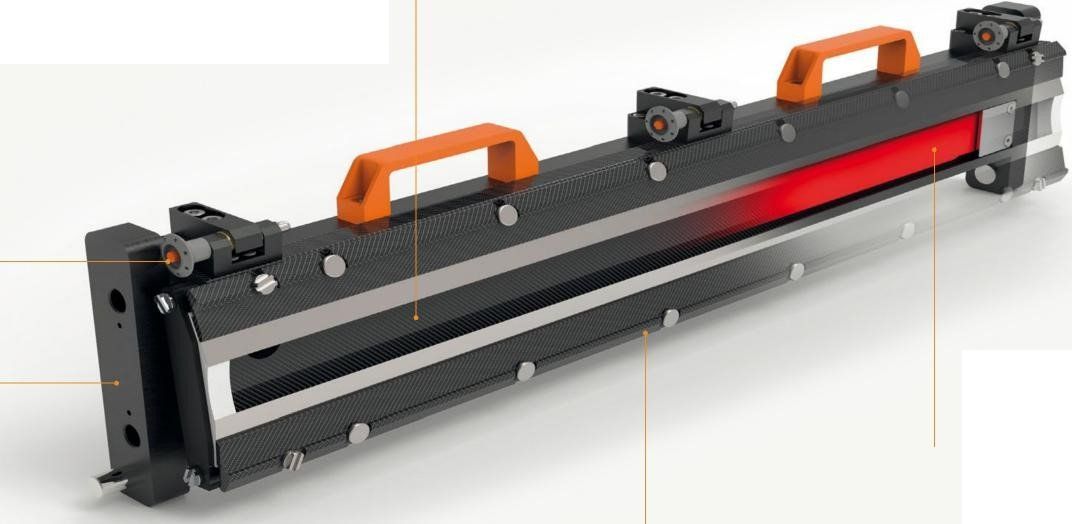
Easy2Remove connection
The doctor blade unit can be removed quickly and reassembled in the machine thanks to the special fixing system on the approach system. Useful for off-machine pit stops
Ultra Smooth Surface
The doctor blade unit can be removed quickly and reassembled in the machine thanks to the special fixing system on the approach system. Useful for off-machine pit stops
Compact and precise
The BFT Carbon approach systems are the most compact and robust available on the market and that can be lodged on label printing machines.
Clamp2Go blade closure
The quick release and spring hooking system of the blade stop slats, allows changing the blades quickly and precisely, avoiding undulations on the blade, thanks to the constant pressure along the entire unit.
Touch2Go pressure
The doctor blade unit approach system, equipped with an aircushion, allows positioning the doctor blade unit in contact with the anilox with a low pressure, along the entire unit, reducing the consumption of blades and lateral seals, guaranteeing an optimal doctoring operation.
Asymmetric and symmetrical profiles of different sizes are available depending on the diameter of the anilox.
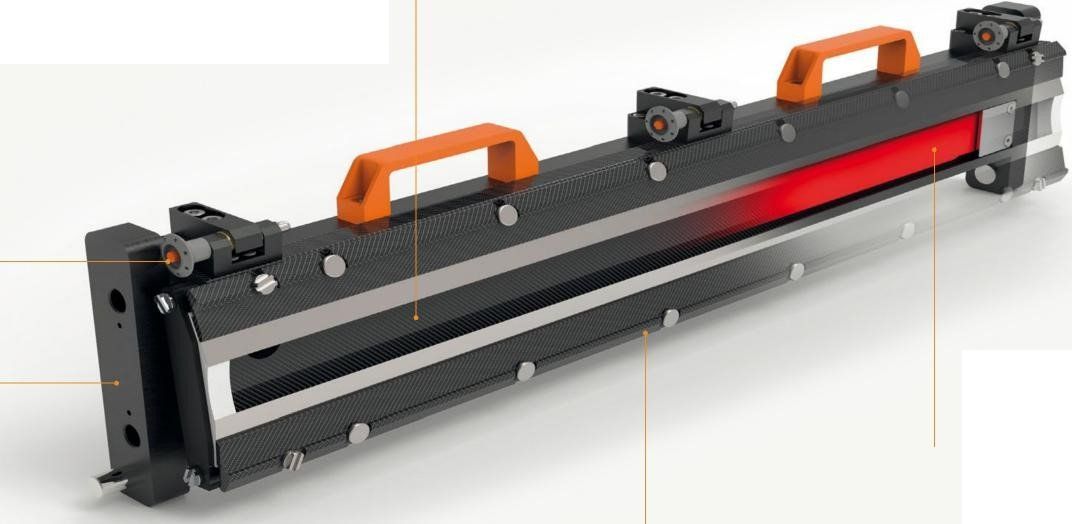
Easy2Remove connection
The doctor blade unit can be removed quickly and reassembled in the machine thanks to the special fixing system on the approach system. Useful for off-machine pit stops
Ultra Smooth Surface
The doctor blade unit can be removed quickly and reassembled in the machine thanks to the special fixing system on the approach system. Useful for off-machine pit stops
Compact and precise
The BFT Carbon approach systems are the most compact and robust available on the market and that can be lodged on label printing machines.
Clamp2Go blade closure
The quick release and spring hooking system of the blade stop slats, allows changing the blades quickly and precisely, avoiding undulations on the blade, thanks to the constant pressure along the entire unit.
Touch2Go pressure
The doctor blade unit approach system, equipped with an aircushion, allows positioning the doctor blade unit in contact with the anilox with a low pressure, along the entire unit, reducing the consumption of blades and lateral seals, guaranteeing an optimal doctoring operation.
Asymmetric and symmetrical profiles of different sizes are available depending on the diameter of the anilox.
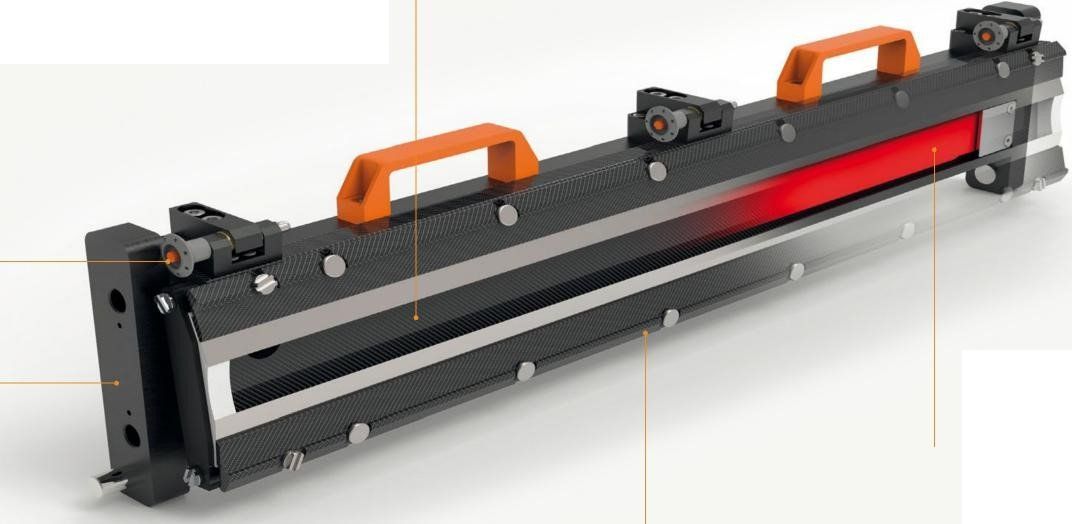
Easy2Remove connection
The doctor blade unit can be removed quickly and reassembled in the machine thanks to the special fixing system on the approach system. Useful for off-machine pit stops
Ultra Smooth Surface
The doctor blade unit can be removed quickly and reassembled in the machine thanks to the special fixing system on the approach system. Useful for off-machine pit stops
Asymmetric and symmetrical profiles of different sizes are available depending on the diameter of the anilox.
Compact and precise
The BFT Carbon approach systems are the most compact and robust available on the market and that can be lodged on label printing machines.
Clamp2Go blade closure
The quick release and spring hooking system of the blade stop slats, allows changing the blades quickly and precisely, avoiding undulations on the blade, thanks to the constant pressure along the entire unit.
Touch2Go pressure
The doctor blade unit approach system, equipped with an aircushion, allows positioning the doctor blade unit in contact with the anilox with a low pressure, along the entire unit, reducing the consumption of blades and lateral seals, guaranteeing an optimal doctoring operation.
Our Partners
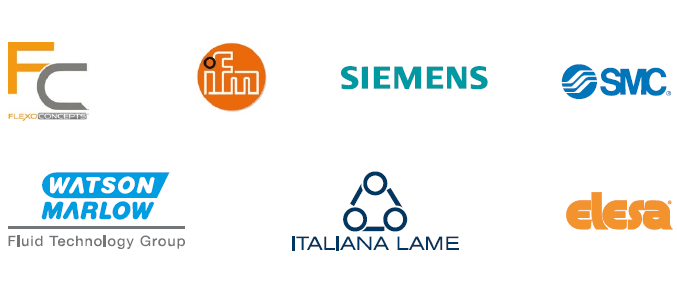